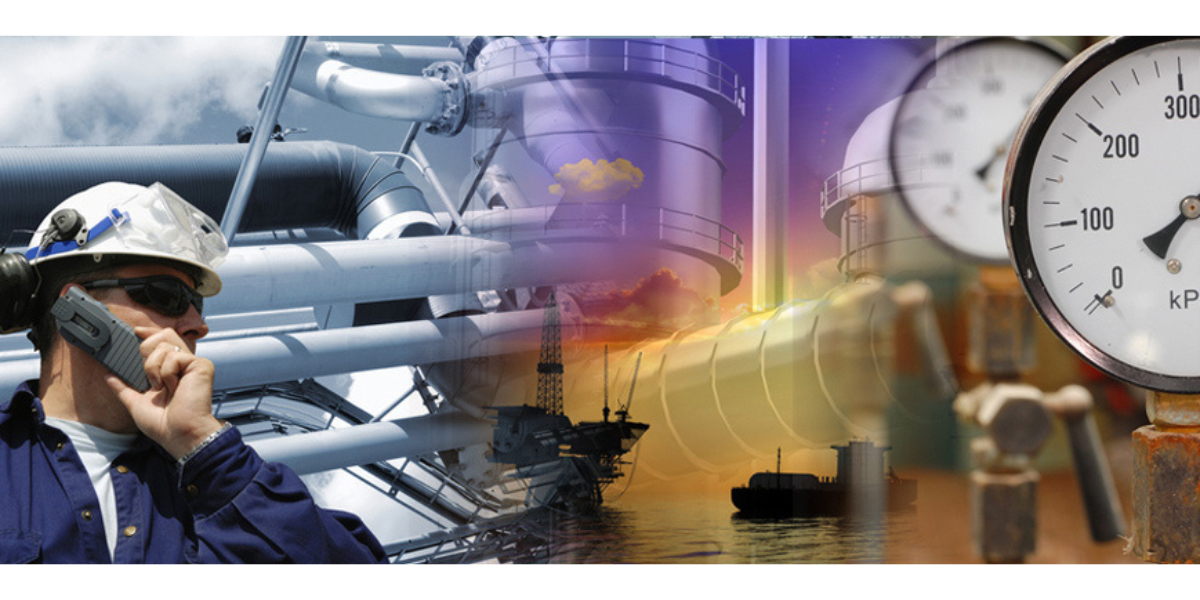
Project Startup & Commissioning
Startup and commissioning in industrial automation is the initializing, testing, and optimizing of an automation system to ensure that it operates effectively and efficiently within a manufacturing or industrial environment. Here’s an overview of the critical steps Exonix follows in this process:
- Preparation: Before startup and commissioning, thorough planning is essential. This includes reviewing the system design, documentation, and specifications to understand the intended functionality and performance requirements. It also involves preparing the equipment, tools, and resources for the commissioning process.
- nstallation: The physical installation of automation components, such as sensors, actuators, controllers, and networking infrastructure, is carried out according to the system design and layout plan. Proper installation is crucial to ensure the reliability and functionality of the automation system.
- Initial Power-Up: Once the hardware installation is complete, the system is powered up for the first time. This initial power-up allows engineers to verify that all components are receiving power and functioning as expected.
- Hardware Testing: After the initial power-up, engineers perform hardware testing to ensure that all components are communicating properly and that there are no hardware faults or malfunctions. This may involve checking wiring connections, verifying sensor and actuator functionality, and troubleshooting any issues that arise.
- Software Configuration: The software components of the automation system, such as PLC programs, HMI interfaces, and SCADA systems, are configured according to the system design and functional requirements. This includes programming logic, setting up alarms and notifications, and configuring communication protocols.
- Functional Testing: Once the hardware and software are configured, engineers conduct functional testing to verify that the automation system performs the intended operations correctly. This may involve running test scripts, simulating production scenarios, and validating system responses.
- Optimization: During the commissioning process, engineers fine-tune the automation system to optimize its performance and efficiency. This may involve adjusting control parameters, optimizing motion profiles, and fine-tuning feedback loops to achieve desired outcomes.
- Validation: After the system has been optimized, validation testing is conducted to ensure that it meets the specified performance requirements and functional specifications. Validation may involve running production trials, collecting performance data, and comparing results against predefined criteria.
- Training: As part of the commissioning process, operators and maintenance personnel are trained on how to use and maintain the automation system effectively. Training ensures that personnel have the necessary knowledge and skills to operate the system safely and efficiently.
- Handover: Once commissioning is complete and the automation system has been validated, it is handed over to the client or end-user for full operation. Documentation, manuals, and support materials are provided to facilitate ongoing operation, maintenance, and troubleshooting.
Overall, startup and commissioning in industrial automation are critical phases in the implementation of automation projects. They ensure that systems are properly configured, tested, and optimized to meet the needs of the manufacturing or industrial process. Effective startup and commissioning improve industrial operations’ productivity, efficiency, and reliability.